Stahl

Stahl ist ein Werkstoff, der überwiegend aus Eisen mit geringem Kohlenstoffanteil besteht. Stahl lässt sich warm oder kalt umformen, er kann also geschmiedet, gebogen, gewalzt und gezogen werden.
Häufig wird Stahl als Eisen-Kohlenstoff-Legierung mit einem Kohlenstoff-Massenanteil von maximal 2 %[1] definiert. Eisen-Kohlenstoff-Legierungen mit höheren Kohlenstoffanteilen werden Gusseisen genannt und sind nicht plastisch umformbar, lassen sich also nicht schmieden oder walzen. Neben Kohlenstoff enthält Stahl immer auch Rückstände von unerwünschtem Phosphor, Schwefel und einige weitere Verunreinigungen. Moderne Stahlsorten enthalten zusätzlich weitere Elemente, die gezielt zulegiert wurden, um die Eigenschaften des Stahls zu verbessern. Entscheidend für die Eigenschaften des Stahls sind Mengenanteile der Begleit- und der nachträglich hinzugefügten Legierungselemente sowie die Kristallstruktur nach Verformung und der Wärmebehandlungszustand.
Stahl ist einer der vielseitigsten Konstruktionswerkstoffe und ist nahezu unbegrenzt wiederverwertbar. Seine Produktion (im Jahr 2016: 1629 Millionen Tonnen) übertrifft die Menge aller übrigen metallischen Werkstoffe zusammen um mehr als das Zehnfache. Stahl ist in großen Mengen und zu geringen Kosten verfügbar. Seine Eigenschaften lassen sich durch Legieren und Wärmebehandeln in weiten Bereichen variieren. Es gibt etwa 3.500 Stahlsorten.[2]
Stahl lässt sich durch Gießen und vor allem gut durch Walzen, Schmieden, Fräsen und Schweißen verarbeiten und hat eine hohe Festigkeit (einfacher Stahl 180 bis 350 N/mm², hochfester Stahl bis weit über 1200 N/mm²)[3], gute Härtbarkeit, Steifheit (E-Modul) und Bruchdehnung.
Kohle und Stahl (Montanindustrie) waren lange Zeit Hauptsäulen der Schwerindustrie. Die moderne Stahlerzeugung wird unter den Gesichtspunkten der CO2-Emissionen weiterentwickelt.
Wortherkunft
[Bearbeiten | Quelltext bearbeiten]Das Wort „Stahl“ entwickelte sich aus dem mittelhochdeutschen stahel, stāl, dem althochdeutschen Wort stahal, dem mittelniederdeutschen stāl, mittelniederländischen stael und dem altnordischen stál, welche sich auf stehen oder stellen zurückführen lassen und als Substantivierung von standhaft und stark aufzufassen sind[4]; daneben die j-Bildung im altsächsischen stehli ‚Axt‘ und altenglischen stīle.[5]
Definitionen
[Bearbeiten | Quelltext bearbeiten]EN 10020 – Begriffsbestimmungen für die Einteilung der Stähle
[Bearbeiten | Quelltext bearbeiten]
| |||
Bereich | Werkstoffe | ||
Titel | Begriffsbestimmungen für die Einteilung der Stähle | ||
Kurzbeschreibung: | Stahl, Definitionen | ||
Letzte Ausgabe | 2000–03-22 | ||
Klassifikation | 01.040.77, 77.080.20 | ||
Nationale Normen | DIN EN 10020:2000-07, ÖNORM EN 10020:2000-06-01, SN EN 10020:2000-07-15 |
In der EN 10020:2000–07 Begriffsbestimmungen für die Einteilung der Stähle wird unter Punkt 2.1 folgendes ausgeführt:
„[Stahl ist ein] Werkstoff, dessen Massenanteil an Eisen größer ist als der jedes anderen Elements, dessen Kohlenstoffgehalt im Allgemeinen kleiner als 2 % ist und der andere Elemente enthält. Eine begrenzte Anzahl von Chromstählen kann mehr als 2 % Kohlenstoff enthalten, aber 2 % ist die übliche Grenze zwischen Stahl und Gusseisen.“
Der Grenzgehalt an Kohlenstoff von 2 % leitet sich direkt aus dem Eisen-Kohlenstoff-Diagramm ab. Bis zu einem Gehalt von 2,06 % kann der Werkstoff bei hohen Temperaturen in der Phase von Austenit vorliegen, der sich gut umformen lässt.[6][7]
Fachliteratur
[Bearbeiten | Quelltext bearbeiten]Die in der Fachliteratur gebräuchlichen Definitionen orientieren sich an der DIN EN 10020 und enthalten alle die Definition als Eisenwerkstoff, meist mit Hinweis auf den Kohlenstoffanteil von weniger als 2 %. Zusätzlich wird aber immer betont, dass Stähle umformbar sind, also durch Schmieden, Walzen und ähnliche Verfahren bearbeitet werden können.
- „… Eisenlegierungen bezeichnet, die weniger als 2 % Kohlenstoff enthalten und die für eine Warmumformung geeignet sind.“
- Bernhard Ilschner, R. F. Singer Werkstoffwissenschaften und Fertigungstechnik: Eigenschaften, Vorgänge, Technologien. 5. Auflage. 2010, S. 431.
- „Eisen-Kohlenstoff-Legierungen mit einem Kohlenstoffanteil i. Allg. unter 2 Gew.-%, die kalt oder warm umformbar (schmiedbar) sind, …“
- H. Czichos, B. Skrotzki, F.-G. Simon: Hütte – Das Ingenieurwissen: Werkstoffe. 2014, S. 24.
- „Eisen-Kohlenstoff-Legierungen, die ohne weitere Nachbehandlung schmiedbar sind, sind Stähle (C ≤ 2 %).“ Der Zusatz „ohne weitere Nachbehandlung“ schließt hier Temperguss aus, eine Gusseisensorte, die nach einer Wärmebehandlung (Tempern) schmiedbar wird.
- Hans-Jürgen Bargel, Günter Schulz (Hrsg.): Werkstoffkunde. 11. Auflage. 2012, S. 181.
- „Stahl ist schmiedbares Eisen …“
- Böge: Handbuch Maschinenbau. 21. Auflage. S. E14.
- „Als Stähle werden praktisch alle verformbaren technischen Legierungen des Eisens bezeichnet.“
- Erhard Hornbogen, Hans Warlimont Metalle: Struktur und Eigenschaften der Metalle und Legierungen. 6. Auflage. 2016, S. 291.
- „… Eisenwerkstoffe darstellen, die sich i. Allg. für die Warmumformung eignen, …“
- Dubbel, 24. Auflage, S. E34.
- „… die im allgemeinen für eine Warmformgebung geeignet sind.“
- VDEh: Werkstoffkunde Stahl – Band 1: Grundlagen, 1984, S. 21.
Technikhistorische Begriffsverwendung
[Bearbeiten | Quelltext bearbeiten]Diese allgemeine, seit dem frühen 20. Jahrhundert gebräuchliche Definition umfasst mit dem Begriff Stahl auch das damals kaum mehr produzierte Schmiedeeisen, das einen geringen Kohlenstoff-Gehalt von meist unter 0,3 % hat. Damit ist es dann nicht härtbar und hat einen anderen Einsatzbereich. Trotz ähnlicher Zusammensetzung wie Stahl ist es aber aufgrund verschiedener Verunreinigungen nicht identisch mit Stahl. Wenn in modernen Werken (ab dem 20. Jahrhundert) im historischen Kontext von „Stahl“ die Rede ist, so ist damit meist „Schmiedeeisen“ gemeint. Selbst in Werken der Technikgeschichte wird für frühere schmiedbare Eisenwerkstoffe der Begriff Stahl verwendet. Der Begriff Schmiedeeisen diente in der Antike als Abgrenzung gegenüber dem Roheisen, das noch sehr stark verunreinigt war, und ab dem Mittelalter zusätzlich gegenüber dem nicht schmiedbaren Gusseisen.[8]
Geschichte
[Bearbeiten | Quelltext bearbeiten]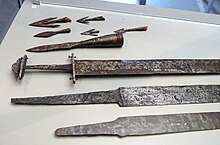
Die frühe Verhüttung von Eisenerz ist bereits für das 2. Jahrtausend v. Chr. im damaligen Hethiter-Reich belegt, wo auch um die Mitte des 1. Jahrtausends v. Chr. einfache schmiedbare Eisenwerkstoffe und erstmals ein einfacher härtbarer Stahl hergestellt wurde.[9] Zu der Zeit wurde das Erz in mit Holzkohle beheizten Rennöfen bei Temperaturen von etwa 1250 °C verhüttet. Der hohe Grad an Verunreinigungen in der Luppe erlaubte nur die Herstellung von Schmiedeeisen geringer Qualität. Genutzt wurde Eisen vor allem für Waffen und Rüstungen sowie für Werkzeuge, weniger in der Landwirtschaft oder als Schmuck.
Im 14. Jahrhundert n. Chr. wurde in Europa der Holzkohle-Hochofen (Stückofen) entwickelt. Er erreichte höhere Temperaturen und benötigte weniger Kohle. Das Eisenerz reagierte darin mit dem Kohlenstoff der Holzkohle. Die Schmelztemperatur lag dank des Kohlenstoffgehalts nun unter der Hochofentemperatur, sodass erstmals flüssiges Roheisen entstand. Die Eigenschaften des Eisens konnten gezielt durch Anlassen, Aufkohlen, Abschrecken und Glühen beeinflusst werden.
In der Industrialisierung wurden die Hochöfen immer mehr durch Steinkohle (Koks) befeuert, die Eisenwerkstoffe günstiger werden ließ und die Produktionsmengen erhöhte. Innerhalb der Produktionstechnik konnten Eisen oder Stahl nun als Konstruktionswerkstoff für Werkzeugmaschinen[10] genutzt werden, die dadurch präziser und leistungsfähiger wurden. Das durch Puddeln gefrischte Eisen wurde anschließend unter dem Schmiedehammer bearbeitet, um die Schlackereste zu entfernen und den Werkstoff homogener zu machen. Dieser Schmiedeprozess hatte ebenfalls großen Einfluss auf die Qualität des Stahls. Erst danach wurde er zu Blechen oder Schienen gewalzt und ermöglichte anspruchsvolle Anwendungen wie z. B. Dampflokomotiven, Schienen, die Griethausener Eisenbahnbrücke und den Eiffelturm.[11][12][13]

Das Bessemer-Verfahren (ab 1864) und später das Siemens-Martin-Verfahren erlauben das gezielte Frischen des Roheisens, um den Kohlenstoffgehalt zu reduzieren.[14] Beim Frischen werden auch unerwünschte Begleitelemente wie Silicium, Mangan, Schwefel und Phosphor durch Zugabe von Sauerstoff verbrannt. Dies erlaubte die Herstellung von qualitativ höherwertigem Stahl, der jedoch wegen des aufwendigeren Prozesses zunächst etwas teurer war. In den vertikal integrierten Stahlkonzernen mit ihren Erzgruben, Hochöfen, Bessemer- oder Siemens-Martin-Hütten und den Walzwerken ging es nun darum, die Kosten für das gesamte Unternehmen zu minimieren.[15] Das Siemens-Martin-Verfahren wurde erst Mitte des 20. Jahrhunderts langsam vom sogenannten Elektrostahl aus Lichtbogenöfen und dem Linz-Donawitz-Verfahren abgelöst.
In der chemischen Industrie wurden bei einigen Prozessen wie dem damals neuen Haber-Bosch-Verfahren zur Herstellung von Ammoniak sehr hohe Drücke und Temperaturen von bis zu 330 bar und 550 °C benötigt. Der am Prozess beteiligte Wasserstoff diffundierte in den Stahl der Reaktorwände, löste den darin enthaltenen Kohlenstoff und verringerte dadurch die Festigkeit des Stahls, was zu Reaktorexplosionen führte. In der Folge entwickelte man hochlegierte Stähle, die ihre Festigkeit nicht über den Kohlenstoff, sondern über andere Legierungselemente erhalten und daher chemisch beständiger sind. Der wichtigste Vertreter ist der austenitische, rostfreie Chrom-Nickel-Stahl. Die neuen Stähle und chemischen Verfahren verhalfen sich somit gegenseitig zum großtechnischen Durchbruch.[16]
Um eine gemeinsame Kontrolle der Kohle- und Stahlproduktion sicherzustellen, wurde 1952 auf französische Initiative hin die Montanunion gegründet. Aus der Montanunion entwickelte sich dann schrittweise die Europäische Union. In der Folge erlebte die Stahlindustrie in der Bundesrepublik Deutschland einen großen Aufschwung. Im Jahr 2008 benötigt die Stahlindustrie in Deutschland etwa 76.500 Mitarbeiter, um rund 46 Millionen Tonnen Stahl herzustellen. Diese enorme Produktivitätssteigerung war nur durch bedeutende technische Innovationen möglich.
Herstellung, Recycling und Ökologie
[Bearbeiten | Quelltext bearbeiten]Herstellung
[Bearbeiten | Quelltext bearbeiten]
Aus Eisenerzen wird Roheisen gewonnen, indem es zusammen mit Koks (entgaste Kohle) in einen Hochofen gegeben wird. Das Koks erhitzt einerseits durch Verbrennung das Erz und dient andererseits als Reduktionsmittel für das Erz, das chemisch gesehen aus Eisenoxid besteht. Das dadurch entstandene Roheisen dient als Ausgangsmaterial für die Stahlerzeugung. Es enthält etwa 4 % Kohlenstoff und verschiedene Verunreinigungen.
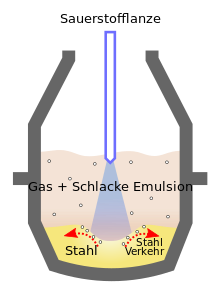
Technisch weit verbreitet (72 % der Welterzeugung, Stand: 2013[17]) ist das Linz-Donawitz-Verfahren (LD-Verfahren). Bei diesem wird das flüssige Roheisen aus dem Hochofen in einen großen, schwenkbaren Behälter gefüllt. Dieser Behälter, der Konverter, fasst ungefähr 300 t flüssiges Roheisen. Die Reaktion, die zur Umwandlung von Roheisen in Stahl führt, ist exotherm. Damit der Konverter durch zu hohe Temperaturen keinen Schaden nimmt, muss er gekühlt werden. Zu diesem Zweck wird zusätzlich zum Roheisen Eisen- bzw. Stahlschrott beigemischt. Die zum Schmelzen des Eisen- bzw. Stahlschrottes nötige Energie entzieht dem Prozess einen Teil der Wärme. Dennoch steigen die Temperaturen im Konverter von ca. 1250 °C auf etwa 1600 °C.
Der Prozess der Rohstahlerzeugung startet durch das Einfahren einer wassergekühlten Sauerstofflanze in die Schmelze. Durch diese Lanze wird reiner Sauerstoff mit einem Druck von etwa 10 bar in die Schmelze geblasen. Er oxidiert die Begleitelemente, die entstehenden gasförmigen Oxide (Kohlenmonoxid, Kohlendioxid und Schwefeldioxid) entweichen durch die Konverteröffnung in den Abgaskamin. Feste oder flüssige Oxide lagern sich an der Oberfläche der Schmelze ab, wo sie zusammen mit zuvor zugegebenem Kalkstein die sogenannte Schlacke bilden. Nach etwa einer halben Stunde ist der Gehalt an Fremdelementen in der Schmelze stark gesunken. Die Schlacke und die Stahlschmelze (jetzt Rohstahl genannt) werden getrennt voneinander aus dem Konverter in Transportkübel gegossen.
Das zweite wichtige Stahlherstellungsverfahren ist das Elektrostahlverfahren. Mit Graphitelektroden werden im Lichtbogenofen Temperaturen von bis zu 3500 °C erzeugt. Da diese Temperaturen nur lokal an den Spitzen der Graphitelektroden entstehen, kann zur beschleunigten Homogenisierung der Temperaturverteilung mit Lanzen Sauerstoff eingeblasen werden. Dadurch wird der Erschmelzungsprozess deutlich beschleunigt und so können ca. 100 t Stahlschrott in ca. einer Stunde erschmolzen werden. Für die Erschmelzung werden der Eigenschrott, der aus der Stahlherstellung stammt, als auch Fremdschrott, z. B. Automobilschrott, eingesetzt. Bereits während der Erschmelzung können Legierungsmittel der Stahlschmelze zugefügt werden. Die verfeinerte Einstellung der gewünschten chemischen Analyse wird im Legierungsofen vollzogen, nachdem die Stahlschmelze in den sogenannten Legierungsstand verbracht wurde. Für kleinere Mengen oder in Gießereien finden Induktionsöfen häufig Anwendung.
Produktionsmengen
[Bearbeiten | Quelltext bearbeiten]
Die historische Produktion von Stahl verlief lange Zeit auf relativ geringem Niveau: Schätzungen zufolge wurden im Mittelalter im deutschsprachigen Raum zwischen 20.000 t und 30.000 t an Stahl jährlich erzeugt.[18] Gegen 1950 überstieg die Weltproduktion erstmals 200 Mio. Tonnen, bis Mitte der 1970er-Jahre stieg sie weiter bis auf 700 Mio. Tonnen und verweilte bis zur Jahrtausendwende mit geringen Schwankungen auf diesem Niveau. Seitdem stieg sie weiter auf über 1000 Mio. Tonnen, wobei der Zuwachs fast ausschließlich auf China zurückgeht.[19]
Weltweit wurden 2016 1629 Millionen Tonnen Stahl produziert. Das ist mehr als das zehnfache aller anderen metallischen Werkstoffe zusammen. Von Aluminium, dem zweitwichtigsten metallischen Werkstoff, wurden 2016 nur 115 Mio. Tonnen produziert. Das mit großem Abstand bedeutendste Herstellerland war die Volksrepublik China mit einem Anteil von 50 Prozent. Größter Produzent nach China ist Japan mit 6,4 %. In der EU werden 10 % und in Nordamerika (NAFTA) 6,8 % der Weltproduktion hergestellt. In Deutschland wurden mit 87.000 Beschäftigten im Jahr 2014 ca. 43 Mio. t Rohstahl hergestellt.[20]
# | Land | Exportvolumen (in Mio. t) | ||
---|---|---|---|---|
2016 | 2018 | 2020 | ||
1 | ![]() |
43,4 | 46,9 | 33,4 |
2 | ![]() |
24,5 | 29,9 | 22,7 |
3 | ![]() |
21,4 | 29,1 | 22,7 |
4 | ![]() |
18,6 | 24,7 | 19,7 |
5 | ![]() |
14,1 | 23,3 | 16,0 |
6 | ![]() |
13,2 | 19,6 | 13,7 |
7 | ![]() |
12,8 | 16,4 | 12,2 |
8 | ![]() |
10,6 | 15,0 | 11,0 |
9 | ![]() |
1,82 | 5,75 | 10,8 |
10 | ![]() |
11,5 | 16,3 | 10,7 |
Weltweit | 301 | 422 | 325 |
Weltweit wurde 2018 grenzüberschreitend Stahl im Gesamtvolumen von rund 458 Millionen Tonnen gehandelt.[21] China war dabei noch vor Japan und Russland das international wichtigste Exportland gemessen an der Ausfuhrmenge. China ist damit der sowohl bei weitem weltgrößte Produzent als auch Exporteur von Stahl.
Ökologie und Recycling
[Bearbeiten | Quelltext bearbeiten]

Eisen als Hauptbestandteil des Stahles ist, auch wenn es korrodiert oder weggeworfen wird, für Umwelt, Tier, Mensch und Pflanzen nicht toxisch. Die Stahlerzeugung ist ein großer Energieverbraucher. Im Jahr 2013 entfielen ca. 18 % des gesamten weltweiten industriellen Endenergieverbrauchs auf den Eisen- und Stahlsektor.[22] Bei der Ökobilanz von Stahl müssen zwei Herstellungsrouten unterschieden werden:
- Primärerzeugung: Bei der Herstellung eines Kilogramms Rohstahl über die Hochofenroute stoßen die besten Hochöfen in Europa ca. 1,475 kg CO2-Äquivalent aus, was schon nahe am theoretischen Limit von 1,371 kg CO2 liegt. Größere Emissionsreduktionen lassen sich dementsprechend nur noch durch völlig neue Produktionsmethoden erreichen.[23] Auch bei der Hochofenroute werden im sogenannten Konverter etwa 20 % Recyclingmaterial (Schrott)[24] eingesetzt.
- Stahlrecycling: Bei der Recyclingroute im Elektrostahlwerk kann gegenüber der Hochofenroute die zur Reduktion des Eisenerzes aufgebrachte, aus Kohle stammende chemische Energie eingespart werden. Das Recycling von Stahl benötigt 60 bis 75 Prozent weniger Energie als die Primärerzeugung.[25] Dies resultiert in ca. 0,75 kg CO2 pro kg Stahl[26], die genaue CO2-Bilanz ist abhängig von der verwendeten Stromerzeugung. Probleme beim Recycling stellen einzelne Fremdstoffe wie z. B. Kupfer dar, das aus Elektrogeräten stammt.
In der Praxis wird Stahl zuerst aus Erz hergestellt und dann oft mehrfach recycelt (einmalig Primärerzeugung und mehrfach Stahlrecycling). Damit ergibt sich ein durchschnittlicher CO2-Ausstoß von etwa 1 kg CO2 pro kg hergestellten Warmbandstahles. Zum Vergleich: Bei der Herstellung von 1 kg Roh-Aluminium werden 10 kg CO2 freigesetzt (bei Verwendung eines durchschnittlichen Energiemixes). Aus geschreddertem Mischschrott kann über Magnetscheider eine Eisenfraktion zurückgewonnen werden. Legierungselemente können, müssen aber nicht beim Recycling entfernt werden. Hochlegierte Stähle werden daher dementsprechend von Metallaufkäufern extra erfasst und vergütet. Hingegen wird das Recycling dünnwandiger, beschichteter, restentleerter Gebinde (Dosenschrott) teilweise als Downcycling bezeichnet.[27]
Stahl ist mit 500 Mio. t pro Jahr der weltweit meistrecycelte Industriewerkstoff. Die Recyclingquote von Stahl liegt bei 70 %,[28] die von einzelnen Stahlanwendungen z. T. bei deutlich über 90 %.[29] Aus der hohen Recyclingquote resultiert auch, dass Stahllegierungsmetalle die Metalle mit der höchsten Lebensdauer sind.[30]
Für den Korrosionsschutz von Eisen und Stahl werden Stoffe eingesetzt, die das Recycling stören, verloren gehen oder als umweltrelevante Stoffe entweichen oder zurückgehalten werden müssen. Dazu gehören insbesondere die Legierungselemente Chrom und Nickel sowie als Beschichtungen Lacke, Zinn (Weißblech) und Zink. In Europa werden daher die Stahlwerksstäube recycelt, um das darin enthaltene Zink zurückzugewinnen.
Die Stahlerzeugung ist für ca. 25 % der CO2–Emissionen im Industriesektor und ca. 8 % insgesamt verantwortlich.[31][32] Um die globale Erwärmung abzuschwächen, verwendet bzw. erprobt die Stahlindustrie eine Reihe von Technologien zur Dekarbonisierung. Dazu gehören die Nutzung von Wasserstoff, die Kohlenstoffabscheidung und -wiederverwendung sowie der breitere Einsatz von Lichtbogenöfen, die mit erneuerbarer Energie betrieben werden können.[33]
Anwendungsbereiche und konkurrierende Werkstoffe
[Bearbeiten | Quelltext bearbeiten]Stahl ist der Standardwerkstoff im Maschinenbau und ein wichtiger Baustoff im Bauwesen. Die Teildisziplin des Bauingenieurwesens, die sich mit den Besonderheiten von Stahlkonstruktionen befasst, ist der Stahlbau. Von dem in Deutschland genutzten Stahl entfielen 2017 35 % auf das Baugewerbe, 26 % auf den Automobilbau, 12 % auf Metallwaren, 11 % auf den Maschinenbau und 9 % auf Rohre.
Stahl wird verwendet für zahlreiche Maschinen, darunter Pumpen, Krane, Förderanlagen, Turbinen oder Fräsmaschinen, für Stahlseile, Brücken und den Hochbau, im Stahlbeton, für Waffen und Werkzeuge aller Art, für Rohre und chemische Apparate, Druckbehälter, Schienen und für viele Fahrzeuge (Landfahrzeuge, Wasserfahrzeuge, Luftfahrzeuge).[34]
Stahl wird auch in Hochtemperaturwärmespeichern eingesetzt.
-
Verschiedene Maschinenteile
-
Stahlseile
-
Brücken
-
Stahlbeton
-
Druckbehälter
-
(Eisenbahn-)Schienen
-
Schiffe und Kräne
-
Hallen
In Industriezweigen, in denen Leichtbauweise als wichtig gilt (insbesondere Fahrzeugbau und Flugzeugbau), können anstelle von Stahl Werkstoffe von geringerer Dichte verwendet werden, beispielsweise Titan, Aluminium, Magnesium, Kunststoffe und Faserverbundwerkstoffe. Die meisten anderen metallischen Werkstoffe haben aber schlechtere mechanische Eigenschaften als Stahl. Der Vorteil der geringeren Dichte dieser Werkstoffe kann durch gezieltes Verwenden von hochfesten Stählen und durch konstruktive Maßnahmen – etwa die Verwendung von dünnerem Blech mit Aussparungen und Sicken – ausgeglichen werden. Faserverbundwerkstoffe haben zwar teilweise eine wesentlich höhere Festigkeit und Steifigkeit in Faserrichtung; Konstruktion und Verarbeitung sind aber deutlich aufwändiger und unterscheiden sich sehr von der metallischer Werkstoffe.
Arten von Stählen und Stahlprodukten
[Bearbeiten | Quelltext bearbeiten]Im Register europäischer Stähle sind 2017 über 2400 Stahlsorten aufgelistet.
Differenziert wird Stahl beispielsweise[35]
- nach Funktion bzw. Verwendung: Werkzeugstahl, Baustahl, Elektrostahl, Panzerstahl, Stahl für den Leichtbau, Offshore-Stahl, Schiffbaustahl
- nach dem Endprodukt: Federstahl, Kettenstahl, Kunststoffformenstahl, Stahl für Druckbehälter, Ventilstahl, Wälzlagerstahl, Formstahl (für Stahlprofile)
- nach Umformverfahren: Stahl zum Kaltwalzen, Stahl zum Tiefziehen
- nach der vorgesehenen Wärmebehandlung: Einsatzstahl, Nitrierstahl, Vergütungsstahl
- nach Legierung: Kohlenstoffstahl, AHSS-Stahl, unlegierter Stahl
- nach Güteklasse: Edelstahl, Grundstahl, Qualitätsstahl
- nach besonderen Eigenschaften: hitzebeständiger Stahl, nichtrostender Stahl, wetterfester Stahl, zunderbeständiger Stahl, säurebeständiger Stahl, wetterfester Baustahl
- nach Temperaturfestigkeit: Kaltarbeitsstahl, Warmarbeitsstahl, Schnellarbeitsstahl
- Sondervarianten: Cortenstahl, Dualphasen-Stahl, Duplexstahl
Einteilung nach Güteklassen (EN 10020)
[Bearbeiten | Quelltext bearbeiten]Nach EN 10020:2000 wird zwischen drei Hauptgüteklassen unterschieden:
- Unlegierte Stähle (unlegierte Qualitätsstähle, unlegierte Edelstähle). Unlegierte Stähle (in Produktbeschreibungen oft umgangssprachlich Kohlenstoffstahl (AHSS), Carbonstahl oder C-Stahl genannt) enthalten als Zusatz überwiegend Kohlenstoff und geringe Mengen an Legierungselementen wie beispielsweise Chrom, Kupfer, Nickel, Blei, Mangan oder Silizium. Je nach Legierungselement wird ein bestimmter Grenzwert[36] nicht überschritten. Sie werden eingeteilt in Stahlwerkstoffe zur späteren Wärmebehandlung sowie solche, die nicht für eine Wärmebehandlung vorgesehen sind.
- Legierte Stähle (legierte Qualitätsstähle, legierte Edelstähle). Mindestens ein Legierungselement erreicht oder überschreitet seinen jeweiligen Grenzwert.
- Nichtrostende Stähle, d. h. Stähle mit einem Massenanteil von mindestens 10,5 % Chrom und höchstens 1,2 % Kohlenstoff
Die Kurznamen der Stähle sind in der EN 10027 festgelegt. Heute werden ca. 2500 verschiedene Stahlsorten hergestellt, von denen etwa 2000 erst in den letzten zehn Jahren entwickelt wurden.
Die Stahlwerkstoffe werden nach den Legierungselementen, den Gefügebestandteilen und den mechanischen Eigenschaften in Gruppen eingeteilt.
Einteilung nach Anwendungsgebieten
[Bearbeiten | Quelltext bearbeiten]Weitere wichtige Eigenschaften für den Anwender sind die Einsatzbereiche und Verwendungsmöglichkeiten der Stähle. Daher ist auch eine Kennzeichnung sinnvoll, aus der diese hervorgeht:[37][38]
- Baustahl – Baustähle machen über die Hälfte der weltweiten Stahlproduktion aus. Sie sind die Standardsorte, die vor allem zum Bauen von Gebäuden und Maschinen verwendet wird, sofern keine besonderen Anforderungen bezüglich Festigkeit, Korrosionsbeständigkeit oder anderen Eigenschaften vorliegen. Es gibt unlegierte (allgemeine/normalfeste) Baustähle und legierte Baustähle. Baustähle haben häufig sehr niedrige Kohlenstoffgehalte.
- Einsatzstahl – Vorgesehen für eine Einsatzhärtung der Randschichten des fertigen Werkstücks. Dadurch steigt der Kohlenstoffanteil, der vorher bei lediglich 0,1 und 0,2 % lag, im Randbereich auf bis zu 0,8 %. Der Kern des Werkstücks bleibt zäh und bruchfest, da nur die äußere Schicht gehärtet und somit spröde wird.[39] Besonders häufig verwendet werden Einsatzstähle für Kleinteile sowie verschleißfeste Bauteile mit dynamischer Beanspruchung.
- Vergütungsstahl – Der Kohlenstoffanteil liegt zwischen 0,1 und 0,6 %. Diese Stähle besitzen eine gute Eignung zur Vergütung, einer speziellen Wärmebehandlung zum Härten beziehungsweise vollständigen Durchhärten des Stahles. Anwendung findet diese Produktionsmethode für Zahnräder.[39] aber auch für hochbelastete Bauteile, wie z. B. Turbinen von Wasserkraftwerken.
- Nitrierstahl ist zur Härtung durch Nitrieren vorgesehen. Der Kohlenstoffgehalt liegt um 0,3 %. Anwendung für auf Verschleiß beanspruchte Teile.
- Werkzeugstahl – Wird zur Herstellung von Werkzeugen, Gesenken und Gussformen verwendet und zeichnet sich durch eine größere Härte aus.
- Nichtrostender Stahl – Diesen gibt es als ferritischen, als austenitischen, als martensitischen und als Duplex-Stahl. Ersterer wird durch Legieren von mindestens 10,5 Prozent Chrom erzeugt. In austenitischen nichtrostenden Stählen ist zusätzlich Nickel legiert. Austenitische Stähle sind bei Raumtemperatur nicht magnetisch.
- Säurebeständiger Stahl – Ab einem Chromgehalt von mindestens 17 % säure- und laugenbeständig; Verwendung: z. B. Abfüllanlagen für Putzmittel.
Einteilung nach DIN EN 10079 – Begriffsbestimmung für Stahlerzeugnisse
[Bearbeiten | Quelltext bearbeiten]Die DIN EN 10079 (Begriffsbestimmung für Stahlerzeugnisse) unterscheidet die Stahlerzeugnisse in flüssigen Stahl, festen Rohstahl und Halbzeug, Flacherzeugnisse, Langerzeugnisse und andere Erzeugnisse.[40]
Flacherzeugnisse haben einen rechteckigen Querschnitt, dessen Breite deutlich größer als seine Dicke ist. Sie werden unterteilt in
- warmgewalzte Breitflachstähle, Bleche und Bänder ohne Oberflächenveredelung, hergestellt durch Warmwalzen von Halbzeug
- kaltgewalzte Bleche und Bänder ohne Oberflächenveredelung, hergestellt durch Kaltwalzen (die Querschnittsverminderung beträgt im Allgemeinen mehr als 25 %), mit den Sonderformen
- Elektrobleche und -bänder mit definierten magnetischen Eigenschaften (kornorientiert oder nicht-kornorientiert)
- Verpackungsbleche und -bänder aus weichem unlegiertem Stahl (ein- oder zweifach kaltgewalzt; als Tafel oder Rolle; z. B. Feinstblech, Weißblech, spezialverchromtes Blech mit 0,17 – 0,49 mm und verzinntes Blech mit über 0,5 mm Stärke)
- Flacherzeugnisse mit Oberflächenveredelung, warm- oder kaltgewalzt, z. B. mit Beschichtung als
- metallische Überzüge durch Schmelztauchen (Feuerverzinken oder Feueraluminieren) oder elektrolytische Metallabscheidung (mit Zink oder Nickel)
- organische Beschichtungen (Lacke, Pulverbeschichtung etc.)
- anorganische Beschichtungen (Email)
- zusammengesetzte Erzeugnisse (plattierte Bleche und Bänder, Sandwichbleche und -elemente).
Nach Materialstärke werden Flacherzeugnisse in Feinblech und -band bis 3 mm Dicke und Grobblech und -band ab 3 mm Dicke unterteilt.
Struktureller Aufbau
[Bearbeiten | Quelltext bearbeiten]Die Mikrostruktur bestimmt bei Stahl, wie bei vielen Werkstoffen, in hohem Maße die mechanischen Eigenschaften, vor allem die Härte und Festigkeit. Die meisten Stähle bestehen neben Eisen und Kohlenstoff noch aus zahlreichen weiteren Elementen, die zumindest als Verunreinigung enthalten sind – die Stahlbegleiter – oder gewollt zulegiert werden, die Legierungselemente. Die Mikrostruktur ist daher relativ kompliziert, beruht aber im Wesentlichen auf der Struktur der reinen Eisen-Kohlenstoff-Legierungen (insbesondere bei un- und niedrig legiertem Stahl). Deren Struktur basiert wiederum auf derjenigen von reinem Eisen.[41]
Eisenatome liegen wie bei allen Metallen im festen Zustand in einer regelmäßigen Anordnung vor. Unter 911 °C befinden sich die Eisenatome in den Ecken eines gedachten Würfels, in dessen Mitte sich ein weiteres Eisenatom befindet. Diese Struktur wiederholt sich in sämtliche Richtungen theoretisch beliebig oft und wird allgemein als kubisch raumzentriert bezeichnet, im Falle von Eisen auch als -Eisen. Oberhalb von 911 °C liegt Eisen in der sogenannten kubisch flächenzentrierten Form vor, bei der wieder in den Ecken eines gedachten Würfels Atome sitzen, aber diesmal zusätzlich in der Mitte jeder Würfelfläche ein weiteres, aber keines in der Mitte des Würfels. Diese Variante wird als -Eisen bezeichnet. Der für Stahl wesentliche Unterschied ist die unterschiedliche Dichte: In der kubisch flächenzentrierten Form sind die Lücken zwischen den Eisenatomen größer; sie können also leichter durch Atome der Legierungselemente besetzt werden.


Bei reinen Eisen-Kohlenstoff-Legierungen befindet sich immer Kohlenstoff in den Lücken zwischen den Eisenatomen. -Eisen mit Kohlenstoffatomen wird allgemein als -Mischkristall bezeichnet, bei Stahl häufig auch als Ferrit (von lateinisch ferrum = Eisen), während das -Eisen mit eingelagertem Kohlenstoff als -Mischkristall bezeichnet wird und bei Stahl Austenit genannt wird nach William Austen. Austenit kann je nach Temperatur sehr viel Kohlenstoff enthalten, maximal 2,06 Massenprozent, während Ferrit nur maximal 0,03 % Kohlenstoff enthalten kann. Die Temperatur, bei der sich Austenit in Ferrit umwandelt, hängt vom Kohlenstoffgehalt ab und lässt sich aus dem Eisen-Kohlenstoff-Diagramm entnehmen. In beiden Fällen kommt es zu einer Mischkristallverfestigung, also einer Steigerung der Festigkeit. Außer im Eisen-Mischkristall kann Kohlenstoff noch in zwei weiteren Formen vorliegen, insbesondere wenn mehr Kohlenstoff vorhanden ist als im Mischkristall aufgenommen werden kann: Grafit und Zementit. Als Grafit werden Bereiche bezeichnet, die nur aus Kohlenstoff bestehen, während Zementit eine chemische Verbindung aus Eisen und Kohlenstoff mit der Formel Fe3C ist. Grafit entsteht vor allem bei langsamer Abkühlung nach dem Gießen oder Glühen, während der harte und spröde Zementit bei schneller Abkühlung entsteht. Sie führen zu keiner Festigkeitssteigerung.
Weitere Legierungselemente können in verschiedenen Formen im Stahl vorliegen:
- Als Mischkristall: Elemente, deren Atome sehr viel kleiner sind als die von Eisen (wie Kohlenstoff, Wasserstoff oder Stickstoff), besetzen die Lücken zwischen den Eisenatomen (Einlagerungsmischkristall). Größere Atome befinden sich statt eines Eisenatomes im Eisengitter (Austauschmischkristall). Auch diese erhöhen die Festigkeit.
- Sie können weitere chemische Verbindungen bilden, häufig zusammen mit Kohlenstoff die Karbide, z. B. Wolframcarbid oder Vanadiumcarbid, teils auch untereinander. Gleichzeitiges Legieren von Schwefel und Mangan führt zur Bildung von Mangansulfid. Manche Elemente verbinden sich auch bevorzugt mit Eisen. Die Wirkung dieser Verbindungen ist im Einzelnen sehr verschieden: Manche sind für die Wärmebehandlung von Bedeutung, andere erhöhen die Härte und Verschleißfestigkeit, andere senken die Festigkeit und verspröden den Stahl.
- Sie können kleine Partikel bilden, die nur aus dem jeweiligen Element bestehen. Dies trifft nur auf wenige Elemente zu darunter Blei, Grafit und Kupfer. Sie verringern meist die Festigkeit.
Eigenschaften
[Bearbeiten | Quelltext bearbeiten]Allgemeine physikalische Eigenschaften
[Bearbeiten | Quelltext bearbeiten]Die Dichte von Stahl beträgt 7,85–7,87 g/cm3 (7850–7870 kg/m3).
Der Schmelzpunkt von reinem Eisen liegt bei 1536 °C, durch Zugabe von Legierungselementen verringert sich in der Regel der Schmelzpunkt von Stahl und liegt bei 2 % Kohlenstoff nur noch bei 1400 °C. Aus dem Eisen-Kohlenstoff-Diagramm ersichtlich, hat Stahl genaugenommen wie die meisten Legierungen keinen genauen Schmelzpunkt: Bei Temperaturen oberhalb der Liquiduslinie (oberste Linie im Diagramm) ist der Werkstoff vollständig flüssig, zwischen der Liquidus- und Soliduslinie (zweitoberste Linie) liegt er teilweise flüssig und fest vor. Erst bei Unterschreiten der Soliduslinie liegt nur noch fester Werkstoff vor.
Die elektrische Leitfähigkeit von Stahl ist etwas geringer als die von reinem Eisen mit 10·106 S/m. So hat Stahl C15 (mit 0,15 % Kohlenstoff) 9,3·106 S/m, Stahl C35 8,6·106 S/m und Stahl C60 7,9·106 S/m. Die Leitfähigkeit sinkt also merklich mit steigendem Anteil von Kohlenstoff, bleibt aber deutlich über der von rostfreiem Stahl mit 1·106 S/m.[42]
Mechanische Eigenschaften
[Bearbeiten | Quelltext bearbeiten]
Stahl gilt als sehr fester, aber auch „weicher“ Werkstoff, während das verwandte Gusseisen als hart und spröde gilt. Festigkeit ist die auf den Querschnitt bezogene Kraft, die der Werkstoff ertragen kann, bevor er versagt (Reißen, Brechen etc.). Bauteile aus Stahl können also hohe Kräfte übertragen. Stahl gilt als „weich“ also verformbar: Bevor Stahl bricht, verformt er sich, wobei diese Verformung bei Stahl sehr groß sein kann. Gusseisen dagegen bricht ohne vorherige Verformung. Stahl hat daher große Sicherheitsreserven gegenüber Bruch, weshalb er bei wichtigen Fahrzeugteilen genutzt wird (Lenkung, Fahrwerk, Antrieb).
Die Festigkeit liegt bei den am häufigsten verwendeten Stählen, den unlegierten Baustählen, zwischen 180 und 350 N/mm². Sie nimmt mit steigendem Gehalt an Kohlenstoff und sonstigen Legierungselementen zu. Das Verformungsverhalten von Werkstoffen wird in Spannungs-Dehnungs-Diagrammen festgehalten. Dabei wird die Kraft auf eine Materialprobe langsam erhöht und die Längenänderung gemessen. Im Diagramm wird die Mechanische Spannung (Kraft geteilt durch Querschnittsfläche) und die Dehnung (Längenänderung relativ zur Ausgangslänge) aufgetragen. Baustähle weisen eine ausgeprägte Streckgrenze auf: Die Spannung steigt zunächst proportional zur Dehnung und fällt dann plötzlich geringfügig ab. Das Maximum der Geraden im Diagramm ist die Streckgrenze, bis zu der Stähle im Gebrauchsfall genutzt werden sollen. Für die Bearbeitung durch Walzen und Schmieden muss sie überschritten werden.
Hochfeste Stähle können Festigkeiten über 1000 N/mm² erreichen. Manche besondere Sorten, wie die für Klaviersaiten, erreichen sogar über 1800 N/mm².[43][44][45] Stahl ist somit weit fester als Holz, Beton und Stein. Auch die auf die Dichte bezogene Festigkeit, die Spezifische Festigkeit, ist bei Stahl sehr hoch gegenüber diesen Werkstoffen. Konstruktionen aus Stahl sind somit bei vorgegebener bzw. erforderlicher Tragfähigkeit leichter. Übertroffen wird Stahl nur noch von einigen Leichtmetallen wie Aluminium, Magnesium oder Titan.[46] Von allen bekannten Werkstoffen zählen Stähle zu denen mit der höchsten Festigkeit. Ähnliche, aber geringere Werte erreichen neben Aluminium-, Magnesium- und Titanlegierungen noch CFKs, mit Kohlenstofffasern verstärkte Kunststoffe.[47]
Die Bruchdehnung, also die Dehnung beim Bruch (Ende der Kurve im Spannungs-Dehnungs-Diagramm), kann bei Tiefziehstahl mit geringer Festigkeit 50 % betragen, höherfeste Stähle (AHSS) haben in der Regel dagegen geringere Bruchdehnungen; Baustähle dehnen sich also sehr weit, bevor sie brechen. Im Gegensatz dazu brechen Gusseisen und Keramik bei Überschreiten der Festigkeit ohne vorherige plastische Verformung.[48]
Der Elastizitätsmodul von gewöhnlichen ferritischen Stählen beträgt 210 GPa (2,1·105 N/mm²). Im Spannungs-Dehnungs-Diagramm ist er als Steigung der Geraden zu erkennen. Der E-Modul ist damit etwas höher als der von Gusseisen (170 GPa) und deutlich höher als der von Aluminiumlegierungen (70 GPa). Übertroffen wird Stahl nur von wenigen Werkstoffen, darunter Hartmetalle (ca. 500 GPa) und Diamant (900 GPa).[49]
Die Härte kann bei Stahl in großen Bereichen variieren und Vickershärten zwischen 80 und 940 HV erreichen. Weichgeglühte Vergütungsstähle erreichen Härten von 150 bis 320 HV (150 bis 300 Brinell, 1 bis 33 Rockwell), vergütete (gehärtete) Vergütungsstähle liegen bei etwa 210 bis 650 HV. Werkzeugstahl erreicht im gehärteten Zustand bis 840 HV. Im Vergleich dazu liegen Kupfer- und Aluminiumwerkstoffe zwischen 40 und 190 HV, während Hartmetalle 780 bis 1760 HV erreichen.[50] Typische Keramiken sind noch härter.
Technologische Eigenschaften
[Bearbeiten | Quelltext bearbeiten]Technologische Eigenschaften beziehen sich auf die Be- und Verarbeitung. Im Einzelnen handelt es sich um die Gießbarkeit, Schmiedbarkeit, Zerspanbarkeit und Schweißbarkeit. Mit Ausnahme der Gießbarkeit sind sie bei den häufig genutzten Sorten gut bis sehr gut.
Gießbarkeit
[Bearbeiten | Quelltext bearbeiten]
Gießbarkeit ist die Eignung eines Werkstoffes, durch Gießen verarbeitet zu werden. Gemeint ist hier vor allem das Formgießen, bei dem die Formen schon die Gestalt der späteren Endprodukte enthalten, nicht das Gießen zu Barren.
Stahl lässt sich vergleichsweise schlecht gießen, weshalb er von allen in der Gießerei verwendeten Werkstoffen einen geringen Massenanteil hat und sowohl von Gusseisen als auch von Aluminium deutlich übertroffen wird, da sich beide viel besser gießen lassen. 2011[51] wurden in Deutschland ca. 220.000 Tonnen Stahl in Gießereien genutzt, während es bei Gusseisen ca. 4,2 Mio. Tonnen und bei Aluminium 840.000 Tonnen waren.
Spezielle Stahlsorten für Gießereien werden als Stahlguss bezeichnet. Er neigt zu Warmrissen, die nur mit gießtechnischer Erfahrung beherrschbar sind. Außerdem ist der Schmelzpunkt mit 1580 °C bis 1680 °C sehr hoch (Gusseisen 1100 °C, Aluminiumgusslegierungen um 600 °C), was zu einem hohen Energiebedarf beim Schmelzen führt und zu hohen thermischen Belastungen der Formen und Anlagen. Stahl neigt beim Formgießen zu Oberflächenanbrennungen mit der Form und es sind große Speiser nötig um den Volumenverlust bei der Abkühlung in der Form auszugleichen. Nach dem Erstarren lassen sich die Speiser nur schwer wieder abtrennen. Gegossene Werkstücke aus Stahl sind wegen des hohen Fertigungsaufwandes etwa dreimal teurer als solche aus Gusseisen, obwohl wegen der höheren Festigkeit weniger Material benötigt wird.[52]
Schmiedbarkeit und Umformbarkeit
[Bearbeiten | Quelltext bearbeiten]
Umformbarkeit ist die Eignung eines Werkstoffes, sich durch die Verfahren der Umformtechnik bearbeiten zu lassen. Das mit Abstand wichtigste Verfahren der Gruppe ist das Schmieden, weshalb auch von Schmiedbarkeit gesprochen wird. Zu der Gruppe zählen aber auch das Biegen, Walzen, Tiefziehen, Fließpressen und viele weitere.
Die Umformbarkeit ist umso besser, je geringer die nötigen Kräfte sind und je stärker sich der Werkstoff verformen kann, ohne zu brechen oder reißen. Die zur Umformung benötigte Kraft wird üblicherweise auf die Querschnittsfläche bezogen und als Fließspannung angegeben. Die maximale Dehnung, die ein Werkstoff ertragen kann, ist die Bruchdehnung.
Bei einfachen Baustählen ist die Fließspannung vergleichsweise gering und die Bruchdehnung sehr hoch. Bei hochfesten Stählen ist die Fließspannung naturgemäß höher, es werden aber auch deutlich festere Werkstoffe geschmiedet, darunter Titan-, Nickel- und Kobalt-Legierungen. Die Bruchdehnung ist meist umso kleiner je fester ein Stahl ist. Eine Ausnahme sind die TRIP-Stähle mit geringer bis mittlerer Fließspannung und hoher Bruchdehnung. Bei den meisten Stahlsorten ist die Fließspannung als gering einzustufen. Dazu zählen neben den Baustählen die Warmarbeitsstähle und Automatenstähle. Aluminium- und Magnesiumlegierungen liegen in einem ähnlichen Bereich. Die Bruchdehnung kann jedoch stärker schwanken: Bei Automatenstählen ist sie sehr gering, bei Warmarbeitsstählen fast genauso gut wie bei Baustählen.
Beim Kaltumformen steigt die Fließspannung und somit auch die nötige Kraft je höher der Umformgrad (die Verformung) ist. Der Effekt wird als Kaltverfestigung bezeichnet und kann genutzt werden um besonders feste Werkstücke zu schmieden. Der genaue Zusammenhang zwischen Fließspannung und Umformgrad wird in Fließkurven festgehalten. Bei höheren Temperaturen sinkt bei fast allen Stählen sowohl die Fließspannung als auch die Verfestigung. Beim Warmumformen steigt die Fließspannung bereits bei geringen Umformgraden gar nicht mehr. Bei Stählen tritt dies bei Temperaturen von etwa 1100 °C auf.[53][54][55]
Zerspanbarkeit
[Bearbeiten | Quelltext bearbeiten]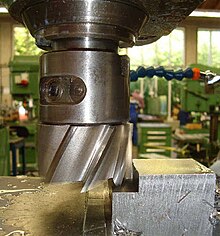
Die Zerspanbarkeit ist die Eignung eines Werkstoffes, sich durch Zerspanen (Fräsen, Drehen, Hobeln, Bohren, Schleifen) bearbeiten zu lassen. Sie hängt ab vom Kohlenstoffgehalt, den sonstigen Legierungselementen und dem Wärmebehandlungszustand. Stähle mit einem sehr niedrigen Kohlenstoffgehalt neigen zum Verkleben mit der Schneide und bilden lange Bandspäne, die sich in der Maschine verfangen können. Sie führen jedoch zu geringen Zerspankräften, aber auch zu schlechten Oberflächen. Bei mittleren Kohlenstoffgehalten (0,2 % bis 0,6 %) gibt es keine Probleme mit Verklebungen. Die Schnittkräfte steigen, die Oberflächen werden besser und die Späne kürzer. Dafür nimmt der Verschleiß der Werkzeuge zu. Stähle mit einem hohen Kohlenstoffgehalt führen zu hohen Kräften und Temperaturen sowie zu einem hohen Verschleiß. Die Oberflächenqualität und der Spanbruch sind jedoch gut. Elemente wie Phosphor, Blei und Schwefel begünstigen die Zerspanbarkeit, festigkeitssteigernde Elemente wie Nickel verringern sie. Im weichen (normalgeglühten) Zustand sind die meisten Stähle relativ gut zu zerspanen, im vergüteten oder gehärteten Zustand ist der Verschleiß dagegen sehr hoch, was teure Werkzeuge aus Schneidkeramik oder Bornitrid erfordert.
Schweißeignung
[Bearbeiten | Quelltext bearbeiten]
Die Schweißeignung gibt an, wie gut sich ein Werkstoff schweißen lässt. Vor allem die un- und niedrig legierten Baustähle lassen sich sehr gut schweißen, was ein wichtiger Grund für ihre weite Verbreitung ist, da Verbinden durch Schweißen deutlich kostengünstiger ist als durch andere Verbindungstechniken wie Schrauben oder Nieten. Höherlegierte Stähle können beim Schweißen problematisch sein. Als grobe Abschätzung, ob ein Stahl geschweißt werden kann, kann das Kohlenstoffäquivalent genutzt werden, das den unterschiedlichen Einfluss der verschiedenen Legierungselemente berücksichtigt. Aluminium lässt sich meist deutlich schlechter schweißen als Stahl.[56]
Veränderung von Stahleigenschaften und Wärmebehandlung
[Bearbeiten | Quelltext bearbeiten]Die mechanischen Eigenschaften des Stahls (Härte, Festigkeit) können auf verschiedene Weisen verändert werden:
- Kaltumformen: Durch Schmieden, Walzen, Ziehen und verwandte Verfahren steigt die Festigkeit bei allen Metallen und Legierungen sofern die Temperatur unterhalb einer werkstoffabhängigen Grenze liegt. Die Verfestigung kann gewünscht sein und gezielt genutzt werden um besonders feste Werkstücke herzustellen, sie kann aber auch unerwünscht sein, wenn bei der Bearbeitung zu große Eigenspannungen entstehen. Durch ein nachträgliches Glühen können die Eigenspannungen abgebaut werden und somit die gewünschten Gebrauchseigenschaften eingestellt werden.
- Legieren: Zulegieren verschiedener Elemente erhöht im Allgemeinen die Festigkeit. Manche Elemente wie Phosphor und Schwefel verspröden den Werkstoff. Blei hat bei Raumtemperatur kaum Auswirkungen, senkt aber die Festigkeit bei hohen Temperaturen. Chrom und Nickel verbessern bei gewissen Mindestgehalten die Korrosionsbeständigkeit.
- Wärmebehandlung: Dadurch können Härte und Festigkeit auf vielfältige Weise geändert werden. Vor der Bearbeitung kann Stahl weichgeglüht werden um die Bearbeitungskräfte zu senken, danach ist Härten möglich um die Verschleißfestigkeit vor dem Gebrauch zu erhöhen. Der Werkstoff kann über den gesamten Querschnitt gehärtet werden, wobei er auch spröder wird, oder nur in den Randschichten, während die inneren Bereiche zäh und fest bleiben.
Die Wärmebehandlungsverfahren werden in mehrere Gruppen eingeteilt:
- (rein) thermische Verfahren: z. B. Glühen
- thermochemische Verfahren: Dabei wird die chemische Zusammensetzung des Stahls geändert, typischerweise nur der oberflächennahen Bereichen
- thermomechanische Verfahren: Sie kombinieren eine mechanische (Walzen, Schmieden) mit einer thermischen Bearbeitung.
Thermische Verfahren
[Bearbeiten | Quelltext bearbeiten]
Thermische Verfahren ändern die Mikrostruktur durch rein thermische Einflüsse, ohne zusätzlich die chemische Zusammensetzung zu ändern und ohne gleichzeitige mechanische Bearbeitung.[57]
- Glühen: Zum Glühen zählt eine Reihe von Verfahren, bei denen die Werkstücke zuerst erwärmt werden, eine gewisse Zeit auf Glühtemperatur gehalten werden und schließlich abgekühlt werden. Verfahrensparameter sind vor allem die Glühtemperatur- und -dauer sowie die Abkühlgeschwindigkeit. Die genauen Ergebnisse hängen mit der jeweiligen Legierungszusammensetzung und ihrem genauen Zustand ab. Vorangegangene Wärmebehandlungen können größeren Einfluss auf das Ergebnis haben.
- Spannungsarmglühen, verringert oder beseitigt durch umformende Bearbeitung entstandene Eigenspannungen und wird bei relativ geringen Temperaturen von 550 °C bis 660 °C für 2 bis vier Stunden durchgeführt. Andere Eigenschaftsänderungen werden vermieden.
- Weichglühen, verringert die Härte, vor allem um die nachfolgende spanende Bearbeitung zu erleichtern. Lamellarer Zementit wandelt sich dabei in eine kugelige Form um.
- Normalglühen (Normalisieren) erzeugt ein gleichmäßiges, feinkörniges Gefüge. Gefügeveränderungen durch vorangegangene Bearbeitungen werden dadurch beseitigt.
- Grobkornglühen vergrößert Körner im Gefüge, was mit einem Abfall der Festigkeit verbunden ist. Es wird vor einer spanenden Bearbeitung angewandt.
- Lösungsglühen verringert ungleichmäßige Verteilungen der Legierungsbestandteile. Durch Diffusion wandern Atome von Bereichen mit hoher Konzentration zu Bereichen niedriger Konzentration. Meist entsteht dadurch Grobkorn, das durch Warmumformung (Schmieden) oder Normalisieren beseitigt werden kann.
- Rekristallisationsglühen dient zur Beseitigung der Kaltverfestigung und verbessert dadurch die Umformbarkeit stark verformter Werkstoffe.
- Härten ist eine Prozessfolge aus Austenitisieren (um 800 °C), Abschrecken (schnelles Abkühlen) und Anlassen (Erwärmen auf 180 bis 300 °C). Durch das Abschrecken wird der Stahl sehr hart, aber auch spröde. Das anschließende Anlassen verringert die Sprödigkeit. Kohlenstoffgehalte ab 0,2 %.
- Vergüten ist mit dem Härten verwandt. Das Anlassen erfolgt bei 450 bis 650 °C, Kohlenstoffgehalte zwischen 0,3 % und 0,8 %.
- Bainitisieren: Erzeugung von Bainit im Gefüge.
- Randschichthärten: Die Randschichten werden dabei schnell erwärmt während die inneren Schichten wegen der begrenzten Wärmeleitfähigkeit kalt bleiben. Varianten sind das Flammhärten, Induktionshärten, Laserstrahlhärten und Elektronenstrahlhärten.
Thermochemische Verfahren
[Bearbeiten | Quelltext bearbeiten]
Sie verändern den Stahl auch chemisch. Folgende Verfahren werden angewandt:[58]
- Aufkohlen erhöht den Kohlenstoffgehalt, vor allem in den Randschichten, was Härte und Festigkeit erhöht.
- Carbonitrieren erhöht den Kohlenstoff- und Stickstoffgehalt in der Randschicht.
- Nitrieren bildet in der Randschicht Nitride (Stickstoffverbindungen).
- Einsatzhärten besteht aus der Folge Aufkohlen, Härten, Anlassen. Die entsprechenden Stähle werden als Einsatzstahl bezeichnet.
- Borieren ist ein Härteverfahren das auf dem Einbringen von Bor basiert.
Thermomechanische Verfahren
[Bearbeiten | Quelltext bearbeiten]Thermomechanische Verfahren basieren auf einer mechanischen Bearbeitung (Schmieden, Walzen) kombiniert mit einer Wärmebehandlung. Von Bedeutung ist das Austenitformhärten, das zur Festigkeitssteigerung dient.[59]
Literatur
[Bearbeiten | Quelltext bearbeiten]- Verein Deutscher Eisenhüttenleute (Hrsg.): Werkstoffkunde Stahl, Band 1: Grundlagen. Springer-Verlag, Berlin/ Heidelberg/ New York/ Tokyo 1984, ISBN 3-540-12619-8, und Verlag Stahleisen, Düsseldorf 1984.
- Verein Deutscher Eisenhüttenleute (Hrsg.): Werkstoffkunde Stahl, Band 2: Anwendungen. Springer-Verlag, Berlin/ Heidelberg/ New York/ Tokyo 1985, ISBN 3-540-13084-5, und Verlag Stahleisen, Düsseldorf 1985.
- Claus und Micah Wegst: Stahlschlüssel – Key to Steel 2010 Nachschlagewerk. Verlag Stahlschlüssel, 2010, ISBN 978-3-922599-26-5.
- Industrieverband Massivumformung: Neue Stähle für die Massivumformung. Inforeihe Massivumformung, Hagen 2012, ISBN 978-3-928726-28-3.
- Theisen Berns: Eisenwerkstoffe. 4. Auflage. Springer, 2013.
Weblinks
[Bearbeiten | Quelltext bearbeiten]- Literatur von und über Stahl im Katalog der Deutschen Nationalbibliothek
- Stahl Informationszentrum
- Stahlseite: Fotografien zu fast allen Verfahren der Stahlerzeugung und Stahlverarbeitung
- Transport-Informations-Service: Fachinformationen zum Transport von Stahl
- Hüttenwerke Krupp Mannesmann Flash-Animation „Wege der Stahlerzeugung“
- Beste verfügbare Techniken – (BVT). Download der BVT-Merkblätter und Durchführungsbeschlüsse. ( vom 17. Juli 2013 im Internet Archive) Bei: Umweltbundesamt.de.
- Patrick Chudalla, Thomas Stahl: Vom Eisenerz zum Stahl. (PDF; 3 MB) Auf www.fh-muenster.de
Einzelnachweise
[Bearbeiten | Quelltext bearbeiten]- ↑ Siehe Abschnitt #Definitionen
- ↑ DER SPIEGEL 1/2022, S. 116, Jörg Römer: Ein Nugget aus der Zukunft
- ↑ The Challenge for Maximum Tensile Strength Steel Cord. In: Nippon Steel Technical Report No. 80, July 1999 (PDF, 333 kB).
- ↑ „Stahl“, in: Wolfgang Pfeifer et al., Etymologisches Wörterbuch des Deutschen (1993), digitalisierte und von Wolfgang Pfeifer überarbeitete Version im Digitalen Wörterbuch der deutschen Sprache, https://www.dwds.de/wb/etymwb/Stahl, abgerufen am 3. Dezember 2024.
- ↑ Kluge. Etymologisches Wörterbuch der deutschen Sprache. Bearbeitet von Elmar Seebold. 25., durchgesehene und erweiterte Auflage. Walter de Gruyter, Berlin/Boston 2011, ISBN 978-3-11-022364-4, S. 875.
- ↑ Wilhelm Domke: Werkstoffkunde und Werkstoffprüfung. 10., verbesserte Auflage, Cornelsen-Velhagen & Klasing, 2001, ISBN 3-590-81220-6, S. 78
- ↑ Grundlagen des Schmiedens und der Wärmebehandlung, Juli 2011. In: messerforum.net
- ↑ Wolfgang König (Hrsg.): Propyläen Technikgeschichte. Band I, Propyläen, Berlin 1997, S. 419–421.
- ↑ Friedrich Cornelius: Geistesgeschichte der Frühzeit. Band 1, Verlag Brill Archive, 1960, S. 132.
- ↑ Wolfgang König (Hrsg.): Propyläen Technikgeschichte. Band 3, Propyläen, Berlin 1997, S. 330.
- ↑ Wolfgang König (Hrsg.): Propyläen Technikgeschichte. Band 3, Propyläen, Berlin 1997, S. 402 f. Ulrich Wengenroth: Eisen, Stahl und Buntmetalle. In: Ulrich Wengenroth (Hrsg.): Technik und Wirtschaft. (= Technik und Kultur. Band 8). VDI-Verlag, Düsseldorf 1993, S. 100–103.
- ↑ Literaturhinweis: R. Sonnemann, S. Richter, H. Wolffgramm, G. Buchheim, H. Eschwege: Allgemeine Geschichte der Technik von den Anfängen bis 1870. VEB Fachbuchverlag, 1981.
- ↑ Ulrich Wengenroth: Eisen, Stahl und Buntmetalle. In: Ulrich Wengenroth (Hrsg.): Technik und Wirtschaft. (= Technik und Kultur. Band 8). VDI-Verlag, Düsseldorf 1993, S. 103.
- ↑ Eckhard Ignatowitz: Chemie für Schule und Beruf. Ein Lehr- und Lernbuch. 4. Auflage. Verlag Europa-Lehrmittel Nourney, Haan-Gruiten 1999, ISBN 3-8085-7054-7, S. 142.
- ↑ Ulrich Wengenroth: Eisen, Stahl und Buntmetalle. In: Ulrich Wengenroth (Hrsg.): Technik und Wirtschaft. (= Technik und Kultur. Band 8). VDI-Verlag, Düsseldorf 1993, S. 115–119.
- ↑ Wolfgang König (Hrsg.): Propyläen Technikgeschichte. Band 5, Propyläen, Berlin, 1997, S. 46.
- ↑ Stahlproduktion: Sauerstoff-Konverter vor Elektroofen. In: industriemagazin.at. 21. November 2014, abgerufen am 26. November 2023.
- ↑ Werkstoffkunde Stahl – Band 1, S. 4 f.
- ↑ Stahlfibel, S. 2.
- ↑ Stahl und Nachhaltigkeit. (PDF) Archiviert vom (nicht mehr online verfügbar) am 8. Juli 2017; abgerufen am 21. Dezember 2015.
- ↑ a b Trade Map - List of exporters for the selected product (Iron and steel). Abgerufen am 7. Februar 2020.
- ↑ Kun He, Li Wang: A review of energy use and energy-efficient technologies for the iron and steel industry. In: Renewable and Sustainable Energy Reviews. 2016, doi:10.1016/j.rser.2016.12.007.
- ↑ Manfred Fischedick u. a.: Techno-economic evaluation of innovative steel production technologies. In: Journal of Cleaner Production. 84, 2014, S. 563–580, S. 564, doi:10.1016/j.jclepro.2014.05.063.
- ↑ Stahlschrottbilanz 2014: Stahlrecyclingwirtschaft musste Rückgang des Gesamtversands um 1,7 Prozent verkraften. ( vom 2. April 2015 im Internet Archive; PDF) bdsv.org, Pressemitteilung, 23. März 2015.
- ↑ Benedikt Müller-Arnold: Produzieren, verkaufen, entsorgen. In: sueddeutsche.de. Abgerufen am 31. März 2023.
- ↑ Multireycling of steel. (PDF) Bei: stahl-online.de. (PDF; 1,03 MB).
- ↑ Lohnt sich Alu-/Weißblech-Recycling? (PDF) Bei: kopytziok.de. (PDF; 92 kB).
- ↑ Steels: Facts, Figures, Environment and Green Steels. Bei: dierk-raabe.com.
- ↑ Sachstandsbericht zum Stahlrecycling im Bauwesen. (PDF; 386 kB) Bergische Universität Wuppertal (PDF).
- ↑ Gerade kritische Metalle haben eine schlechte Ökobilanz. In: springerprofessional.de. 5. Juli 2022, abgerufen am 31. März 2023.
- ↑ HOW CLEAN IS THE U.S. STEEL INDUSTRY? Energy Use and CO2 An International Benchmarking of Energy and CO2 Intensities. IEA, 2019, archiviert vom (nicht mehr online verfügbar) am 15. Mai 2021; abgerufen am 15. Mai 2021 (englisch).
- ↑ Frank Wunderlich-Pfeiffer: Stahlherstellung mit Wasserstoff geht in den Testbetrieb. In: www.golem.de. 7. Oktober 2020, abgerufen am 15. Mai 2021.
- ↑ Alexander Otto, Martin Robinius, Thomas Grube, Sebastian Schiebahn, Aaron Praktiknjo: Power-to-Steel: Reducing CO2 through the Integration of Renewable Energy and Hydrogen into the German Steel Industry. In: Energies. Band 10, Nr. 4, 2017, S. 451, doi:10.3390/en10040451.
- ↑ Stahlinstitut VDEh (Hrsg.): Stahlfibel, Verlag Stahleisen, 2007, S. 162.
- ↑ Eintrag Stahl, BiBuch – Zweisprachiges Informationsportal für Industrie und Technik; abgerufen im März 2019.
- ↑ Unlegierte (allgemeine) Stähle, Grenzwerte. Abgerufen am 28. Dezember 2022.
- ↑ B. Ilschner, R. F. Singer: Werkstoffwissenschaften und Fertigungstechnik. 5. Auflage. Springer, 2010, S. 438 f., 441–445.
- ↑ Hans-Jürgen Bargel, Günter Schulz (Hrsg.): Werkstoffkunde. 11. Auflage. Springer, 2012, S. 239–284.
- ↑ a b C-Stahl Produktdatenblatt ( vom 17. Dezember 2010 im Internet Archive), ThyssenKrupp Steel Europe, abgerufen im Juli 2013.
- ↑ Dr.-Ing. Hans-Joachim Wieland: Information Erzeugnisformen (PDF) S. 1, Stahl-Zentrum; In: stahl-online.de. Abgerufen im Oktober 2019.
- ↑ Hans Berns, Werner Theisen: Eisenwerkstoffe. 4. Auflage. Springer, 2013, S. 3–15.
- ↑ Metallische Werkstoffe – Physikalische Eigenschaften
- ↑ nssmc.com (PDF)
- ↑ H. Czichos, B. Skrotzki, F.-G. Simon: Das Ingenieurwissen – Werkstoffe. Springer, 2014, S. 66.
- ↑ Patent US9266642B2: Steel wrapped pressure vessel. Angemeldet am 27. November 2012, veröffentlicht am 23. Februar 2016, Anmelder: Wirerough Cylinders LLC, Erfinder: Amit Prakash et al.
- ↑ B. Ilschner, R. F. Singer: Werkstofftechnik und Fertigungstechnik. Springer, 2010, S. 433 f.
- ↑ H. Czichos, B. Skrotzki, F.-G. Simon: Das Ingenieurwissen – Werkstoffe. Springer, 2014, S. 59.
- ↑ Hans-Jürgen Bargel, Günter Schulz (Hrsg.): Werkstoffkunde. 11. Auflage. Springer, 2012, ISBN 978-3-642-17716-3, S. 241, 248.
- ↑ H. Czichos, B. Skrotzki, F.-G. Simon: Das Ingenieurwissen – Werkstoffe. Springer, 2014, S. 62.
- ↑ H. Czichos, B. Skrotzki, F.-G. Simon: Das Ingenieurwissen – Werkstoffe. Springer, 2014, S. 71.
- ↑ Günter Spur (Hrsg.): Handbuch Urformen. Hanser, 2014, S. 16.
- ↑ Alfred Herbert Fritz, Günter Schulze (Hrsg.): Fertigungstechnik. 11. Auflage. Springer, 2015, S. 24, 34.
- ↑ Eckart Doege, Bernd-Arno Behrens: Handbuch Umformtechnik. 2. Auflage. Springer, 2010, S. 438–440.
- ↑ Hartmut Hoffmann, Reimund Neugebauer, Günter Spur (Hrsg.): Handbuch Umformen. Hanser, 2012, S. 253.
- ↑ Werkstoffkunde Stahl – Band 1: Grundlagen. 1984, S. 564–615, insb. 564 f., 567, 576.
- ↑ B. Ilschner, R. F. Singer: Werkstoffwissenschaften und Fertigungstechnik. 5. Auflage. Springer, 2010, S. 387.
- ↑ Alfred Böge (Hrsg.): Handbuch Maschinenbau. 21. Auflage. Springer, 2013, S. E35–E40.
- ↑ Alfred Böge (Hrsg.): Handbuch Maschinenbau. 21. Auflage. Springer, 2013, S. E40 f.
- ↑ Alfred Böge (Hrsg.): Handbuch Maschinenbau. 21. Auflage. Springer, 2013, S. E41f.